LEAN-mõtlemisest räägitakse viimasel ajal palju. 5S-tehnika on tuttav ilmselt paljudele tootmisettevõtetele ning 8 raiskamise mudelist on kuulnud tõenäoliselt enamik tootmisjuhte või -planeerijaid. Kas info levik on tekitanud olukorra, kus kõik arvavad, et teavad, millest räägivad, kuid konkreetseid meetodeid lihtsalt ei kasuta?
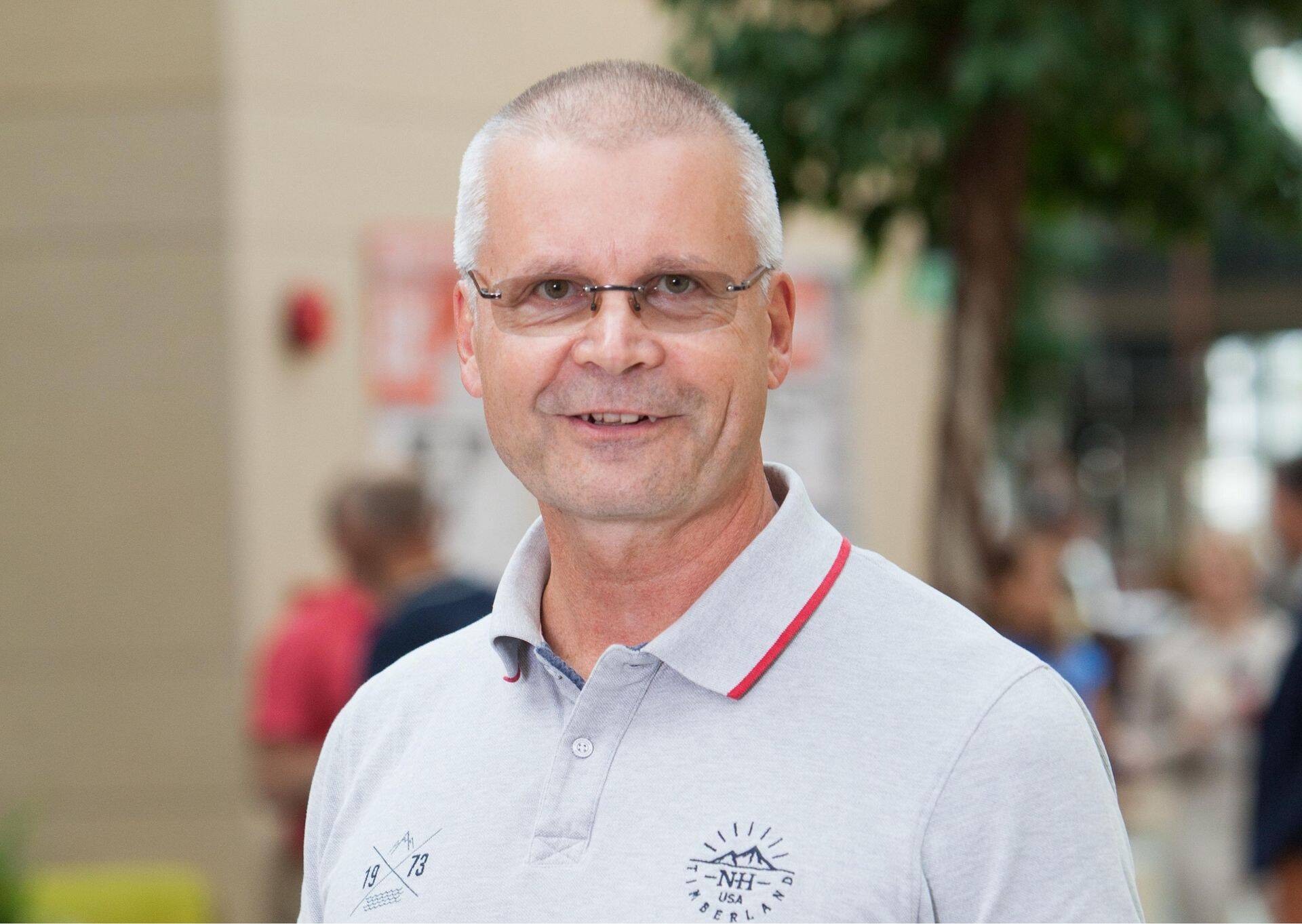
- Koolitaja Jari Kukkonen
- Foto: Äripäev
Koolitaja Jari Kukkoneni sõnul mõistavad tootmisettevõtted hästi, et protsesside efektiivsus tuleb aeg-ajalt üle vaadata, et tootmisvõimsus oleks maksimaalselt kasutatud. “Teoorias saadakse sellest aru, aga tihti jääbki kõik ainult tõdemuseks,” toob Kukkonen välja LEAN-juhtimist puudutava probleemi.
Järgneb intervjuu Jari Kukkoneniga.
Miks peaks palju leierdatud meetodeid tõsiselt juurutama hakkama?
Artikkel jätkub pärast reklaami
On selgemast selgem, et laovarusid on alati vaja nutikalt juhtida, et need liiga suureks ei kasvaks. Samuti peab protsesside efektiivsust aeg-ajalt üle vaatama, et tootmisvõimsus oleks maksimaalselt kasutatud ja ei tekiks tööd häirivaid pudelikaelu.
Teoorias saadakse sellest aru, aga tihti jääbki kõik ainult tõdemuseks ja reaalsuses neid protsesse kriitilise pilguga üle ei vaadata. Sagedaseks vabanduseks on ajapuudus – selleks, et viia sisse kardinaalseid muudatusi või võtta erinevad protsessid algosadeks lahti, kulub esmalt meeletu aeg.
Isegi kui selle aja võtmine tundub igapäevaste tegemiste kõrvalt võimatu, siis tuginedes varasematele praktikatele, on hiljem tänu sellele ajutisele pingutusele reaalselt võimalik võita 25% aega juurde. Kujuta nüüd ette – see on tervelt üks tööpäev nädalas!
Tulekul!
Tootmisjuhtimise kool
Kestus 6 eraldiseisvat päeva, millest 4 päeva veedetakse erinevates tootmisettevõtetes, et õppida parimaid praktikaid ja tajuda siiani ainult teoreetilisi teadmisi ka reaalses elus.
Aitab osalejatel leida võimalikud protsessid oma ettevõttes, mida parendada või ümber korraldada, et tootmist tõhusamaks muuta ja selle abil jõuda paremate tulemusteni kogu ettevõtte väljavaates.
Koolitaja Jari Kukkonen
Vaata lisa ja registreeri
SIIN.
Kuidas saavutada vähemaga rohkemat?
Masinate efektiivsus, protsesside analüüs, arengujuhtimine, kvaliteedijuhtimine – olenemata sellest, kas toodad kosmeetikakreeme või rasketööstuse masinaid, probleemid on ikka täpselt samad.
Olenemata mahtudest kulub keskmises tootmisettevõttes 20–30% kontrollimiseks ja vigade parandamiseks. Võttes arvesse asjaolu, et tööjõud muutub aina kallimaks ja ka logistikavaldkond on kiires muutumises, siis on ümbertöötlemisest ja tühja töö tegemisest tekkiv ressursi raiskamine järjest suurem probleem.
Täiesti iganenud on arusaam, et inimestel peab alati midagi teha olema. Võtame näitena luubi alla mööblitööstuse: juhul kui meistril parasjagu midagi teha pole, siis valmistab ta ette diivanikarkasse. Ühel hetkel tuleb ju ikka tellimus ja siis on seda vaja. Tegelikult on alati kiirem ja kordades odavam valmistada tellimuseks uus karkass, mitte otsida vanade seast. Tihti on siis vaja ka midagi ümber teha ja see on taas pigem peavalu, kui hästi ettevalmistatud töö. See on kõigest üks näide sellest, kuidas mõni juurdunud loogika võib tegelikult osutuda ressursi raiskamiseks.
Teine ilmestav näide tänasel päeval on liigne töötlemine. Tahetakse esmamuljena esitleda maksimaalset kvaliteeti ning tihti hüpata üle oma varju ja pakkuda tooteid või teenust, mida klient tegelikult üldse ei vaja.
Artikkel jätkub pärast reklaami
Ütleme, et klient tellib näidistootena laua. Selleks, et kindlasti jõuda suure tellimuseni ja osutuda valitud tootjaks, viimistletakse see üks laud peensusteni, lihvitakse ja värvitakse ka laua alumine pind. See tõesti jätab hea mulje ja klient esitabki mahuka tellimuse.
Kuna tootmise mõttes on aga äärmiselt ebamõistlik kõiki laudu ka altpoolt lihvida ja värvida ning ega see ka kliendile suurt lisaväärtust loo, siis on kaks võimalust. Esiteks jätta see tegemata ja loota, et klient ei pea seda probleemiks või teiseks panna aur siiski ka alumistele pindadele, jäädes sellega võib-olla ajahätta ja loota, et seetõttu kliendiga probleeme ei teki.
Kogu selle näite mõte on juhtida tähelepanu ootuste upitamise aspektidele, kus tegelikult võiks kokku hoida.
Vältimaks hilisemaid ümbertöötlemisi ja konflikte, ei tasu kliendi ootusi kunagi ajada kõrgemaks, kui reaalne lõpptulemus olema saab. See kõik on tootja endi kätes.
Olulise aspektina tasub aeg-ajalt meelde tuletada tööjaotuse parendamist. Väga paljudes ettevõtetes on edupöördele hoogu andnud intellekti raiskamisele punkti panemine.
Kui keevitaja peab endale mõnikord ise komponente otsima või üksikutel kordadel laost ise asju tooma, siis ei juhtu veel midagi. Aga kui tema tööprotsessi kuulubki kogu varustuse komplekteerimine ja lao vahet jooksmine, siis on midagi valesti.
Igaüks oskab ümmargust asja punktist A punkti B veeretada, aga igaüks, kes oskab veeretada, ei oska keevitada. Ülekvalifitseeritus lihtsate tööde jaoks on andestamatu raiskamise vorm niivõrd kompleksses sektoris, nagu seda on tootmine.
Seotud lood
Kraanade, materjalikäsitlusmasinate ning lisaseadmete müügi ning hooldusega tegelev ScanBalt Crane OÜ tähistab tänavu oma 25. tegutsemisaastat. Veerand sajandit on ettevõte olnud tegev valdkonnas, kus on määrava tähtsusega nende esindatavate seadmete kvaliteet, innovaatika ja tõhusus, pikaajaline koostöö ning partnerite usaldus.